- Description This Used John Deere 33 Integral Rotary Tiller Operators Manual provides operator information for operating and maintaining your John Deere 33 Integral Rotary Tiller. Used John Deere 244E Loader Parts Manual John Deere 5-Speed Bicycle Operators Manual Check out these John Deere 33.
- You searched John Deere tractor manuals for '33 Rotary Tiller': Manual Price; No 2 Swath Fluffer Parts Manual, 10 pages: $39.94 $33.95 (SAVE 15%)! 62 Bulldozer Operators Manual, 24 pages: $39.94 $33.95 (SAVE 15%)! 250 Spracart Sprayer Operators Manual, 124 pages: $39.94 $33.95 (SAVE 15%)! 33 Bale Elevator Parts Manual, 26 pages: $43.47 $36.95.
- Rebuilding a Deere 33 Tiller August 22, 2012. I'd been looking for a John Deere number 33 tiller for my garden tractor for couple of years. In my area they come available only once in a while and they're usually priced pretty high for their (poor) condition. Since this piece of machinery weighs a couple hundred pounds, buying one from out of state isn't really something I'd pay to have shipped.
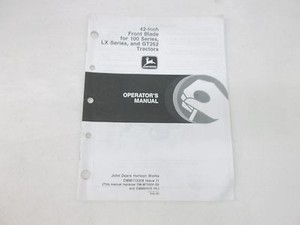
HOME Jim's Garage |
Craftsman Tiller Manual
Rebuilding a Deere 33 TillerAugust 22, 2012
I'd been looking for a John Deere number 33 tiller for my garden tractor for couple of years. In my area they come available only once in a while and they're usually priced pretty high for their (poor) condition. Since this piece of machinery weighs a couple hundred pounds, buying one from out of state isn't really something I'd pay to have shipped. However, I keep hoping that one will come my way. To increase my chances, I've had a saved Ebay search for a 33 tiller for quite a while. I get an email from Ebay when a tiller comes up within two hundred miles from me. Not many hits on this search, but I keep looking.
I was quite surprised when I received the email for a tiller with a buy-it-now price of $100. I was more surprised when the location of the tiller was less than 15 miles from my home. It even came with the original manual. No questions asked, I bought it.
I went to pick up the tiller on a Saturday morning. It seems that the seller had purchased an old Deere 140 H3 to restore and it had come with an amazing assortment of attachments. A couple of plows, a rare seeder, two cultivators, a front snow blade and the tiller. Since he wasn't interested in gardening, he was selling off the stuff he wouldn't use. By selling off the unwanted stuff, he had already made back more than the price of the 140 and all the attachments and was now just looking to make sure that the tiller was going to someone who would appreciate it. Yes, that was me. Sometimes I'm just lucky, but it did take me a couple years of waiting to land this deal.
It happened to be an early tiller complete with a brass serial tag. Serial number is 2549, so it's a very early one made for a Deere 140. The tiller was made before Deere changed from a 3/4' shaft to a one inch one for the upper sprocket. The one inch shaft would be preferable, but I'm not complaining.

I finally have a model 33 tiller. | A bit rusty, but a tiller none-the-less. |
Rebuilding a Deere 33 Tiller - part 2 September 22, 2012. 46' / 48' Mower Deck Just a quick side note about my 46' mowing deck that I couldn't find online and thought that it might help someone in the same situation. Problem: The belt from the PTO to the mower deck was jumping off the deck pulley.
Disassembly:
When Susie and I got home, I used my engine hoist to unload the tiller and get it up on the bench. Due to the large amount of rust on the tiller, I figured that I'd need to start working on the rusted bolts sooner rather than later. I spritzed all the nuts and bolts with a mixture of 50/50 ATF and acetone. A couple days later I tried some disassembly. Some of the nuts broke free and some needed more spritzing. When I got to the point of trying to remove the bar that sets the attachment width, I found that the outer bolt came off easily, but the inner one wouldn't budge. I spritzed the threads some more and waited a couple days and tried again.
I wasn't having much luck removing the inner nut with my open end wrenches, so I tried it with a 15 inch adjustable wrench and promptly broke the spreader bar. Apparently I am stronger than I thought I was (unlikely). The force I applied with the 15' wrench sheared the bar by the threads just after the nut. Crap. However, the situation is not as bad as it could be. The design of this bar is pretty simple; 1/2' round stock with a bent end and a hole for a cotter pin, a U shaped section to go around the pulley nut, then a long straight section with some 1/2-13 tpi threads on the end. I figured that this would be easy enough to make, so I didn't bother looking to buy one. I later found out that it was no longer offered by Deere, so I guess I have no choice but to fabricate it. I proceeded to take apart everything that wasn't rusted stuck.
Although it doesn't look like it in the picture, the chain tensioner is broken. The pin that holds the spring has broken away from the tensioner face. | The tiller drive chain is dry and stretched and the clutch assembly doesn't seem to have moved in a while. |
I stripped off the top chain case and found that one of the clutch disks was trashed but the rest of the clutch assembly looked OK. I'm not quite sure what happened to the outboard disk. It looked to me that the disk hadn't been centered when the assembly was cinched down. The inside circular bore of the disk had been cut and looked egg shaped rather than circular. Strange. Whatever the reason that this occurred, it couldn't be trusted. I added two clutch disks to my parts list. More spritzing and some heat from my Oxy-Acetylene torch got the tiller down to the driven chain case and the tiller tine assemblies. This tiller has extensions on both sides and I was beginning to wonder if/how the tine assemblies would come apart.
A little more rust here too. | The tiller shroud needs a little help and has a couple missing flaps. |
The answer is that they wouldn't come loose easily. Breaking the tine carriers free of the tine shaft was not fun. In fact, I'd put it up there with one of the toughest disassembly jobs I've done on any mechanical unit and I've worked on a lot of stuff. That said, I did most of my wrenching in Southern California and we didn't see too much rust out there, but this thing was a beast to strip down.
To get started removing the tine carriers, I pulled all 4 pins from both sides of the carriers after soaking them with penetrant for a few days. However, the carriers wouldn't budge off of the lower tine shaft. I tried heat. I tried and broke a Snap-on gear puller finger in the process. Darn! I used a big hammer, heat and an air hammer. Nothing worked. It was time to do some research and maybe do some thinking outside the box.
A shot of the left tines. | And the right. Both sides were really worn out. |
When I did some searching for possible ways to remove the tine carriers, I came across what I consider to be a great suggestion. The suggestion was to till some ground with the pins that hold the tine carriers to the shaft removed. By putting rotational strain on the tine carriers, it just might break them free from the main shaft. Unfortunately, I already had the tiller too far apart to try this.
I ended up hooking up both ends of the tine shaft to my engine hoist and tried to pull it apart. No luck initially, but by the third time I heated the tine carrier to red heat and soaking it in PB-Blaster and ATF when it cooled a bit, it finally started to pull free. More heat and with some persuasion from an air hammer, it finally popped off. Only one more tine carrier and two more extensions to go.
The second carrier was stuck tighter than the first, but I got it off with only two heatings. Here's how:
I suspended the tine assembly and chain case from my 2 ton engine hoist with a chain attached to a long bolt passed through one of the tine shaft pin holes. I wrapped another chain around the legs of the hoist and bolted it to the other side of the tine shaft. By pumping up the hoist, I could put pressure on the tine carrier against the main shaft. I used the 2 ton position on the hoist so I could get the most pulling force possible.
All I need to do is pull the tines. | Using the engine hoist to exert pulling pressure. |
Since my tiller has extensions on both sides, there's an additional shaft outboard of the main tine assembly on both sides. On the tine carrier tube, there are three holes for pins. The inner two attach the tine carrier to the main shaft. The outboard hole/pin attaches to the shaft that goes to the tine extension. Looking at the exploded view on the Deere parts page, it appeared that there might be a bit of space between the two shafts inside the tine assembly. I figured it was less than 3/8'. My thought was that with the pin in the extension shaft, hammering on the shaft might move the tine assembly down the main shaft toward the sprocket. If I could move the tine assembly tube even a fraction, I could then use a drift inserted through the pin hole to move it back to its starting position. If I kept repeating this process, I could work the penetrant further into the tube and shaft and loosen the rusted bond.
It worked. Relax the tension, hammer the shaft, use a drift to center the tine carrier on the shaft and repeat. After three or four repetitions, I reheated the shaft, let it cool and tried again. Finally while applying tension from the engine hoist, the tine assembly popped and moved about an inch. I released the tension and hammered it back to the starting position after dousing it with more penetrant. The next time I applied pressure with the engine hoist, the tine assembly popped free of the shaft.
It had only taken about three weeks time and five or six separate visits to the shop to get the tine carriers off. Persistence pays off.
To remove the tine extensions and shafts from the main tine carrier, I used more penetrant, heat and my 20 ton hydraulic press. Too bad that the whole tine assembly wouldn't fit in the press as 20 tons of force works a lot better than two tons applied by the engine hoist. I will say that they make a heck of a noise when they pop free. Once I had all the pieces separated, I used a file and some Emory cloth to clean the rust from the extension shafts.
So the tine carriers were removed, but I was also having trouble getting the main two-sheave pulley off of the shaft that attaches to the angle drive. I tried putting the whole assembly in my hydraulic press, then blocking the underside of the pulley and trying to press the shaft out. All I succeeded in doing was to bow the pulley. I was afraid to put more pressure on the shaft for fear of putting a permanent bend in the pulley, so I figured I'd think about it some more while I cleaned parts.
Sometimes stepping away from a problem helps me come up with another approach. While I cleaned, I remembered that the bevel gear on the inside of the angle drive was held on by a circlip. I wondered if I removed the circlip and gear whether the shaft and pulley would slide out the other side. Yep. In less than five minutes I had the shaft with pulley attached in my hands. Now I could properly brace the underside of the pulley and use the hydraulic press to push the shaft out. Another few minutes work on the press and the shaft and pulley were apart. Needless to say, I was pretty pleased.


Cleaning and Repairs
One of these days I will get a media blaster and blast cabinet for the shop. I really could have used it on this project. However, one makes do with what one has. I washed the worst of the grime off the various parts in a plastic tub, then moved each part into my solvent tank to be cleaned some more. From there each part was either sanded or stripped using an assortment of wire wheels and sanders. All of the parts were then wiped down with Jasco Prep & Primer to convert the remaining rust into black oxide so that the parts could be painted.
I did have a little sheet metal repairing to do on the center tiller flap. Apparently the original owner had gotten both extension flaps hung up on stumps or what-not over the years and they had been ripped off. in the process, all four of the attaching holes on the main flap were ripped out or cracked. To fix these, I cut some sheet metal of the same thickness as the flap and brazed them in place to re-form the square carriage bolt holes. I ground the welds down to (fairly) flat and coated them with Jasco to etch the metal for painting. I'm not really as concerned with doing body shop quality finishing here as I am with getting the piece to function. After all, this is a implement that will get pretty beat up by using it as prescribed. As for the missing parts, I'll look for some extension flaps, but if none show up, I'll probably make up some replacements out of the sheet metal I have on hand.
Broken holes left side. | Broken holes right side. |
Sheet metal cut to fit. | Another key cut and flux applied. |
Key brazed in place. | Repairs are ground down. |
As I said above, the chain tensioner in the drive case was broken. It also had some pretty deep grooves where the chain had run along it un-lubricated for quite a while. My Deere dealer said that this part was no longer available, so I decided I'd repair it as best as I could. The semi-circular rod that holds the spring that pushes against the chain would be easy enough to braze back on. To repair the grooves, I'd fill them with braze (60% silver), then add a piece of Teflon or Delrin to make the chain slide easier. Many motorcycle primary chain tensioners use a facing rather than letting the steel chain ride on a steel tensioner. I'm guessing that using a facing and actually lubing the chain once in a while will make this repair last quite a while.
Broken tensioner. | Tensioner held in the welding vise. |
Flux is added to grooves on tensioner face so I could braze them somewhat flat again. | Rod was brazed to tensioner on both sides. All I need to do now is to face it with Teflon or Delrin. |
Parts Order
For some of the bearings and the tines I needed, I decided to go with aftermarket parts where I could to save some money. Here's the partial list. Note that if you have a later model tiller with the 1' top shaft, your bearings will be different than my 3/4' shaft model bearings (SA204-12).
Tiller tines - 7 each (tiller has both extensions)
http://www.maximmfg.com/
Maxim Mfg. Part No. 130762 (JD PN M43480) right hand tine - price $15.95 each
Maxim Mfg. Part No. 130763 (JD PN M43481) left hand tine - price $15.95 each
Maxim does carry the welded assemblies but that brought the price from about $225 to $400 so I decided to re-use the carrier shafts and just weld new tines on to them.
Bearings / Seals / Chain / Clutch Disks
http://www.thebigbearingstore.com/
2 - JD9274 Lower ball bearing - SA206-20 -- 1-1/4' Insert Bearing Small OD (Pre-lube) $8.70 each
2 - JD9217 Upper ball bearing SA204-12 -- 3/4' Insert Bearing (Pre-lube) $6.15 each
2 - M42512 Outer angle drive bearing 1630RS Radial Ball Bearing 3/4' Bore $3.33 each
2 - JD9325 No seal bearings - inner angle drive bearings - sourced from Deere $13.65 each
2 - AR90860 Seals for angle drive - sourced from Deere $11.26 each
#50 Chain and link kits - sourced from Tractor Supply
2- M151902 - Clutch Disk - sourced from Deere $13.10 each
The tiller tines from Maxim Mfg came pretty quickly after I placed the phone order. I found that they're not real quick to respond by email, but did eventually did respond to my email after I had already placed the phone order. The tines are stamped with the name Empire and look to be pretty nice in quality. Out of the 14 tines, two on each side need to be welded to the main carrier and one on to each extension. The remainder are bolted on. We'll see how the welding goes.
Pretty big difference in size. Looks like the previous owner got a lot of use out of this tiller. | Fourteen tines - Seven each of left and right. |
Reassembly
Since the angle drive and main pulley sheave were the last pieces to be removed, they'd be the first to re-assemble. I had painted the angle drive Deere yellow, but decided to leave the cover unpainted and just polish it up a bit.
I started by installing the two open (unsealed - JD9325) bearings after packing them with wheel bearing grease. I used an aluminum bearing and seal installer and tapped them home. Moving from the inside to the outside of the case, I installed the two AR90860 seals. The new seals were of a different style than the ones I took out. The old ones had a metal shell on both sides and the new ones only had the shell on one side. The open side (cupped side) is installed toward the inside of the housing. I packed some grease in the cupped area and drove them in. The M42512 bearings follow the seals. Again, I used the bearing installer and tapped them home with a plastic faced hammer.
I installed the center circlips on both shafts and slid them in from the outside of the case toward the inside. Once the shafts protruded from the inside bearings by an eighth inch or so, I attached both bevel gears. Do note that if you install the shafts too far past the inner bearings, you won't be able to get the gears on. On my angle drive, 1/8' past the inside bearings seemed to be the perfect distance. Once the gears were in place, I tapped the shafts the rest of the way through. This process would be easier if I had three hands, but wasn't too bad with the two hands I had available. Once the gears were seated, I then installed the parallel (square) keys and some new circlips to hold the gears in place.
The older tillers (mine) call for gear oil as the lubrication of choice for the angle drive and the newer tillers call for 'corn head' lubricant. Older units have two ports on the angle drive cover - one with a 90° pipe fitting to add oil and a pipe plug to check the level. Newer models have no ports at all.
Right or wrong, I did something different. I used a mixture of hypoid gear oil - 85w-140 weight and wheel bearing grease. I used about three ounces total mixed 2/3 grease and 1/3 oil. My reasoning was that the bevel gears had a bit of wear and the grease+oil would help keep them a bit quieter. I also felt that using the thicker mixture would help prevent leaks past the seals later in the angle drive's life. I'll let you know how that works out in a decade or so. Once assembled, the drive felt silky-smooth when turned. So far, so good.
Inside open bearing is greased and installed. Old seal on left and new one (with grease) on right. | Seal is installed cup side down with bearing tool. A large socket would do in a pinch. |
Outer sealed bearing is installed. | The process is repeated for the other bearings. |
With the shafts barely protruding, the gears are added. | Shafts are tapped all of the way through and keys are added. |
Assembled and ready to install. |
I still have a lot to do on this tiller, so I'll be updating this page as I progress on the rebuild. I am hoping that I will have the tiller done before the end of October 2012, so I can get started on a tilling a much larger garden for next year. We do like the sweet corn we've grown this year and want much more.
Tiller Page 1 | Tiller Page 2 | Tiller Page 3 |
John Deere 33 Tiller Manual
© Fager 8-22-12
John Deere 33 Tiller Manual
2032R JOHN DEERE TRACTOR, ROTARY TILLER AND MOWER DECK - $28999 (North Royalton)
NEW 2032R UTILITY TRACTOR-ONLY $28,999 – (440) 241-1370 0% for 60 Months Financing -6 YEAR POWER-TRAIN WARRANTY 2032R John Deere and 220R Loader 61” Bucket and48” 647 Rotary Tiller and 60” Auto-Connect Mower Deck• Drive over auto-connect deck – SUPER EASY• Quick ...
John Deere 272 Rotary mower John Deere 72' 3-Point Grooming Mower - $400 (Moyock)
John Deere 272 Rotary Cutter John Deere 72' 3-Point Grooming Mower/ Finishing / Finish DeckUp for sale is this American made John Deere 272 Rotary Cutter John Deere 72' 3-Point Grooming Mower. Deck has a bad spindle hub assembly and will need replacement. This part can be found on eBay for a ...
John Deere MX6 Rotary Cutter - $4,000 (Fairbanks)
Available NOW!John Deere MX6 6ft Rotary CutterNow Just $4,000.00 (Usually $4,850.00)This machine is Used.Domed shape top deck is smooth and easy to clean. 3-point hitch hookup provides more strength. Front and rear chain shields offer safety. Standard st ...
John Deere 400 Rotary Hoe, Cultivator - $700 (TX - Crockett)
John Deere 20' Rotary Hoe, Model 400 Mounted On 20' JD 85 CultivatorDISCLAIMERThis Item was not Functionally Tested and no guarantees on condition or operability Sold 'As Is, Where Is.’ John Deere 20' Rotary Hoe, Model 400 ...
New John Deere MX10 Rotary Cutter - $9199 (Lake City)
New John Deere MX10 Rotary Cutter- 10' Cutting Width- Minimum 40 PTO Hp Required- Pull Type- 5 Year Warranty on Gearboxes- 1 Year Bumper-To-Bumper Warranty- 4' Wide x 1/2' Thick Blades- Laminated Tires- 1 Year Bumper-To-Bumper Warranty- 5 Year Gearbox Warranty ...
New John Deere MX7 Rotary Cutter - $4199 (Lake City)
New John Deere MX7 Rotary Cutter- 84'- 1'-9.5' Cutting Height- 2' Cutting Depth- Cat 2 Hitch (Cat 3 Convertible)- Laminated Puncture Resistant Rear Tire- Minimum 40 PTO HP- Front and Rear Chains- 1 Year Bumper-To-Bumper Warranty- 5 Year Gearbox Warranty ...
New John Deere E15 Rotary Flex WingCutter - $14999 (Jasper, Ga)
New John Deere E15 Flex Wing Rotary Cutter-Cutting Width: 15ft-Cutting Diameter: 2 in.-Tractor PTO Range: 50 hp-Transport Width: 9.1 ft @ Wing Wheels-Deck Thickness: 11 GaugeContact Adrian WoodruffJohn Deere, Kubota, TYM, Toro, Exmark, Dixie Chopper, G ...
New John Deere E15 Rotary Flex WingCutter - $14,999 (Jasper, Ga)
New John Deere E15 Flex Wing Rotary Cutter-Cutting Width: 15ft-Cutting Diameter: 2 in.-Tractor PTO Range: 50 hp-Transport Width: 9.1 ft @ Wing Wheels-Deck Thickness: 11 GaugeContact Adrian WoodruffJohn Deere, Kubota, TYM, Toro, Exmark, Dixie Chopper, G ...